Results
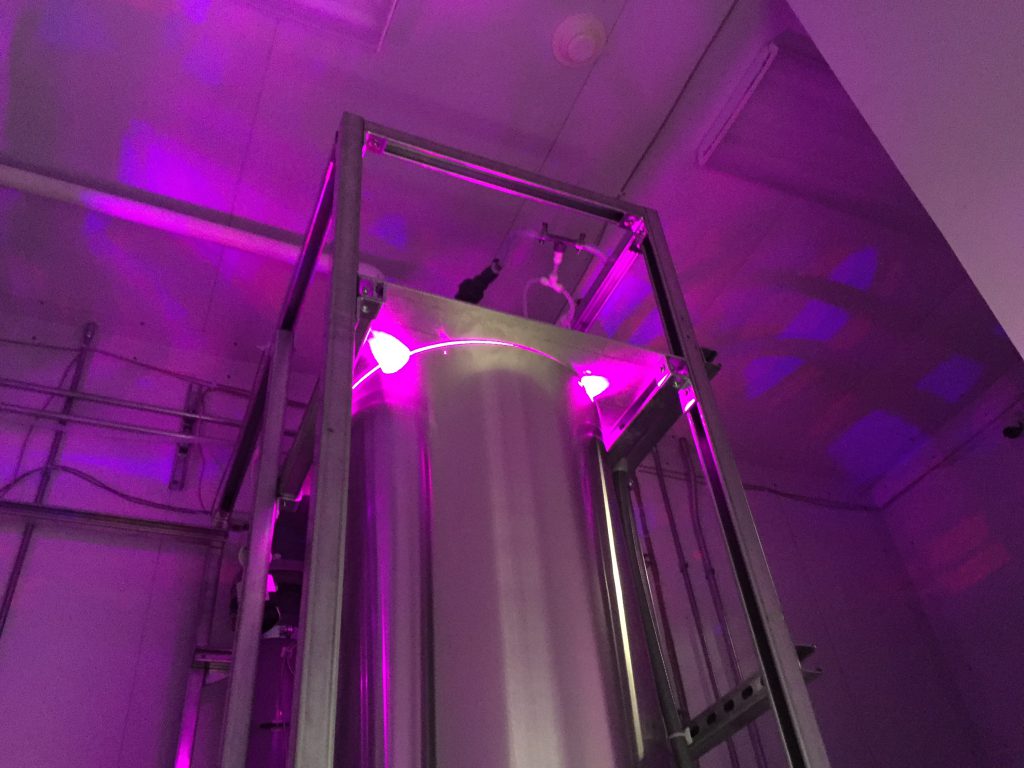
2010 Utah State University Tests – Self Funded
- Stable algae growth
- CO2 absorption estimates ±35%
2015 / 2016 Michigan State University Test – Self Funded
- Sustained production – 5+ months
- Stable algal production rates
- CO2 absorption from boiler flue gas
- Energy balance estimates
- Algae production cost estimates
- Water consumption estimates
2017 / 2020 Michigan State University – DOE Funded
- Started January 2018 with helical coil reactor
- 33 consecutive months of sustained operation completed
- New scalable design built and tested for 3 months
- Testing completed in September 2020
- Final report issued in 2021
2021-2023 Present Joint venture
- Formed Pacific AgriTec, LLC
- Validation testing in California
- Patents filed